Modular Homes Versus Site-Built
Choosing the right construction method for your home can be challenging, especially if you're looking for affordable options. We'll help you make the right choice.
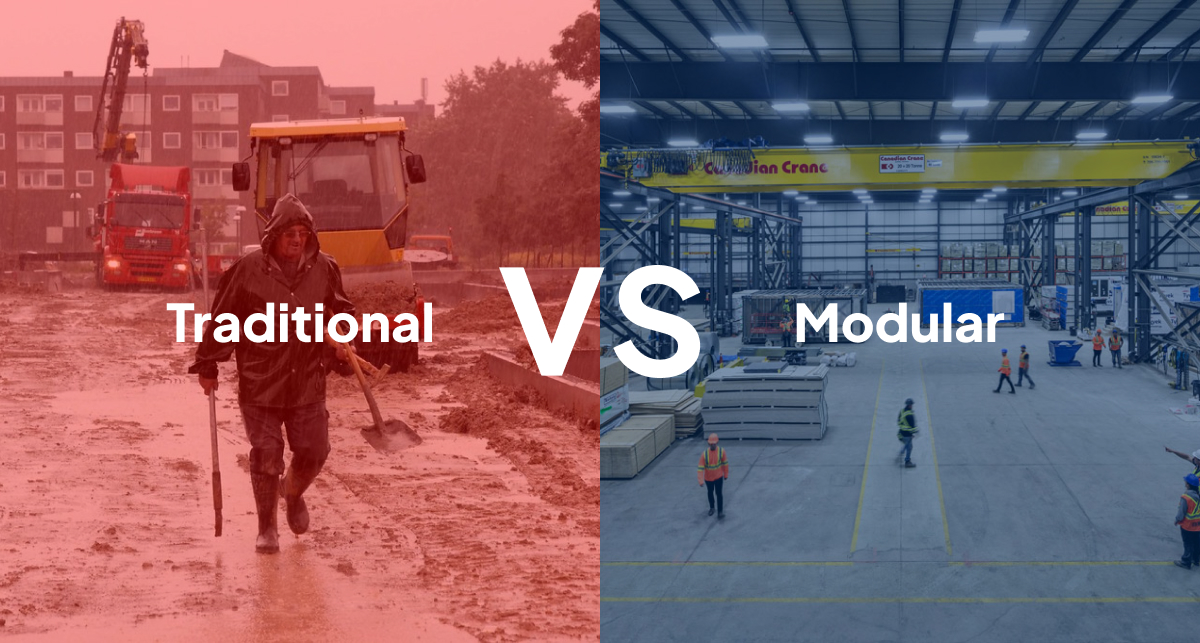
Choosing the right construction method for your home can be challenging, especially if you're looking for affordable options. One homeowner faced frustration when their dream house experienced innumerable delays due to bad weather and labor shortages, driving up costs and stretching timelines.
Prefab modular homes offer an efficient and affordable alternative, promising faster build times and reduced weather-related issues. Positioned in the factory setting, these homes minimize the impact of site constraints, providing a controlled environment that enhances quality and precision. Meanwhile, traditional site-built homes boast customization and adaptation to unique site conditions, albeit with potential delays and higher waste. Understanding these differences will guide your decision-making process.
Speed and Efficiency
When it comes to modular construction, a notable advantage is the simultaneous progress of site preparation and building assembly, drastically reducing construction timelines. Indoor production mitigates weather-related delays, ensuring a seamless and efficient building process.
For traditional construction, the process relies heavily on sequential phases and on-site labor, often subject to weather interruptions and other unforeseen delays. Despite setbacks, traditional methods offer adaptability in design and materials, which may require more time but can result in highly customized structures tailored to specific client needs.
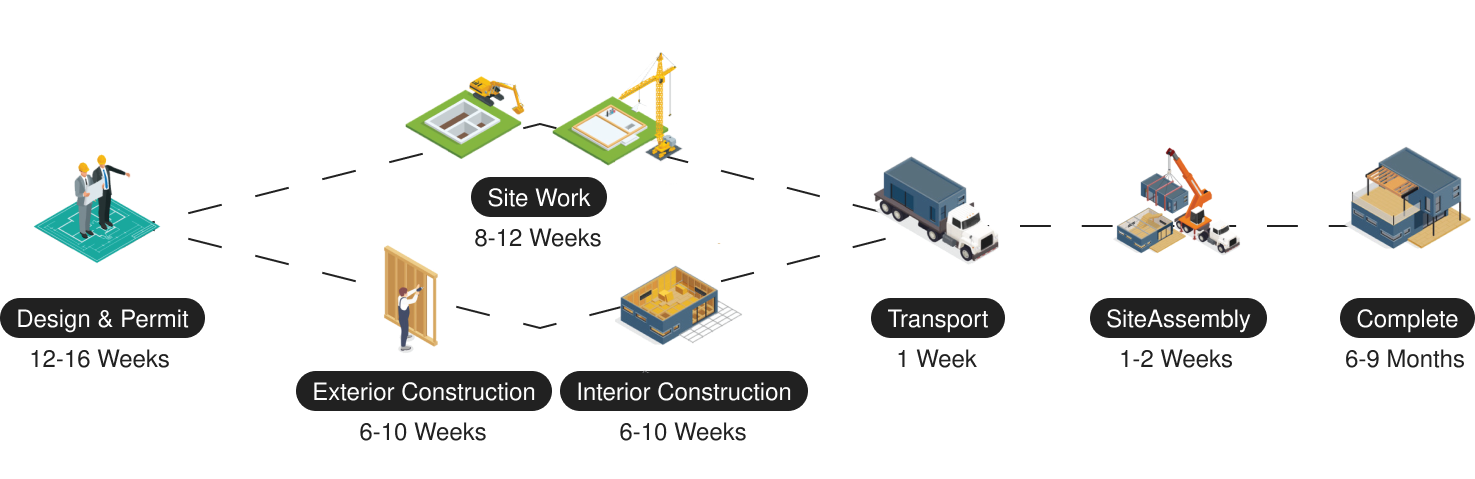
Simultaneous construction
Modular homes leverage simultaneous construction—site preparation and building assembly occur concurrently, expediting completion times.
Simultaneous construction minimizes weather delays and promotes energy-efficient building practices, which often plague traditional on-site methods.
With parallel processes, modular construction significantly reduces overall project timelines, providing homeowners quicker access to their completed homes. The factory setting ensures that critical components are built without interruption from external factors.
This dual-track approach not only enhances efficiency but also maximizes resource utilization, ultimately delivering high-quality homes in less time.
Weather-Resilient Building
Weather-resilient buildings can withstand various environmental challenges, offering reliable protection against extreme weather conditions and natural disasters.
In modular construction, the factory environment fosters a controlled building process, isolating materials and labor from weather-related disruptions. This ensures that components such as walls, roofs, and insulation are constructed under optimal conditions, significantly enhancing their durability and resistance to weather damage.
Furthermore, modular homes can be designed with high-performance materials and construction techniques that enhance resilience. For instance, using impact-resistant windows, reinforced framing, and advanced roofing systems can mitigate the effects of high winds, heavy rains, and other extreme weather events.
Traditional construction, on the other hand, requires adherence to specific local building codes tailored to the region's climate conditions. While the flexible nature of on-site construction allows for bespoke weather-resilient features, it also necessitates precise attention to sealing, insulation, and structural integrity to ensure the home withstands environmental stresses. Adopting best practices in both construction methods can lead to structures with exceptional weather resilience and longevity.
Cost and Waste Management
Modular construction provides significant cost savings, a reflection of its streamlined assembly process, where bulk purchasing and efficient material usage reduce expenses. This contrasts sharply with traditional construction's susceptibility to budget overruns and increasing material costs.
In terms of waste management, modular homes excel due to their factory setting, where precision cuts minimize waste. Factories can repurpose or recycle excess materials, reducing the environmental footprint. Site-built homes, conversely, often generate more waste and are more susceptible to damage from weather exposure, contributing to higher overall waste and cost.
Bulk material savings
Modular homes often use bulk materials.
Buying materials in bulk offers cost savings. This bulk purchasing is possible due to the efficient, centralized nature of the factory setting, which allows for more accurate material estimates and reduces the need for excess ordering. Consequently, manufacturers can pass on these material savings to homeowners.
Smaller, custom orders can be costlier.
Bulk purchasing minimizes material shortages and overruns. By reducing the likelihood of shortages, the construction process experiences fewer delays, which is crucial for adhering to timelines. Additionally, efficient material usage ensures less wastage.
This approach to material procurement emphasizes cost-efficiency, sustainability, and reduced environmental impact, aligning with 2023's high standards for modern homes. Modular homes hence provide a compelling case for bulk material savings, presenting a financially and environmentally sound option for discerning homeowners.
Reduced on-site waste
Modular construction significantly minimizes on-site waste compared to traditional building methods.
- Factory precision: Controlled environments lead to more accurate material usage.
- Efficient material cuts: Reduced scrap generated during factory assembly.
- Minimized environmental impact: Less waste leads to a smaller carbon footprint.
- Recyclable materials: More opportunities for recycling within a factory setting.
- Better inventory management: Less over-ordering and mismanagement of materials.
As a result, homeowners benefit from a cleaner site and a more environmentally friendly building process.
This reduction in waste aligns well with modern sustainability practices.
Quality and Design Precision
Modular homes, constructed within factory settings, adhere to exacting standards with reduced risk of weather-related delays.
Due to controlled environments, these homes ensure precise building techniques and consistent quality control measures, which traditional site-built homes might lack. This results in fewer construction defects.
This meticulous “factory-built” versus “site-built” approach extends to the impeccable precision in modular home design.
Controlled environment benefits
A controlled environment offers unmatched consistency.
By constructing homes in a factory setting, quality control is significantly enhanced. Each stage of construction occurs under stringent supervision, adhering to precise standards and guidelines. Moreover, materials are stored in optimal conditions, ensuring they remain in perfect condition before use. Consequently, this contributes to the durability and longevity of the final product.
Weather conditions play no role here.
Unlike traditional site-built homes, modular homes do not suffer from delays caused by adverse weather. Rain, snow, or extreme temperatures can halt on-site construction, causing delays and potential damage to materials. In contrast, the factory-controlled environment guarantees that construction continues uninterrupted, adhering to projected timelines while preserving material integrity.
Ultimately, the controlled environment in modular home construction translates to superior efficiency, less waste, and consistent quality. This results in higher overall satisfaction for homeowners seeking durable, precision-built residences that are both cost-effective and environmentally friendly.
High-quality materials
Modular homes leverage high-quality materials sourced and assembled under controlled conditions. This meticulous process ensures components meet stringent industry standards, contributing to the overall durability and longevity of the home.
Materials are stored in optimal conditions before use.
This protection prevents damage from weather or pests, common problems in traditional construction.
Factory settings use advanced technology for precise cuts.
Better-fitting components reduce gaps and potential weak points. This increases energy efficiency and structural integrity.
In traditional construction, exposure to the elements can compromise material quality. Modular construction avoids this issue, leading to superior overall quality.
Ultimately, modular homes benefit from consistent material quality not always achievable on-site. This translates into a longer-lasting, more reliable final product.
Market Perceptions
Perceptions of modular homes vary significantly, often shaped by historical associations and regional market trends. Traditionally, these homes were viewed as lower quality, which continues to influence some buyers despite advances in modular construction techniques and materials.
In contrast, traditional site-built homes enjoy a reputation for superior craftsmanship and longevity. This perception, whether accurate or not, can lead to higher resale values. However, as awareness of the high standards and benefits of modular homes increases, market perceptions are slowly shifting to recognize their true value.
Resale value considerations
For homeowners, resale value is a critical factor when choosing between modular and traditional site-built homes.
- Perceived Quality: Traditional homes often have a higher perceived quality which can influence buyers.
- Market Trends: Regional trends can impact the desirability and value of both types.
- Flexibility in Design: Customizable features in site-built homes may appeal more to potential buyers.
- Longevity Perception: Traditional homes are often perceived to have better longevity and offer more customizable floor plans, affecting market value.
While modular homes can be cost-effective, perceptions of quality can impact resale values negatively.
In contrast, traditional homes usually command higher market values due to established perceptions of quality and craftsmanship.
Public Perception Shifts
Public perception of modular homes is evolving, primarily driven by advancements in construction technology and design innovation. Increasing awareness of sustainable construction practices is also contributing to this shift. Modular homes, once stigmatized as low-quality, are gaining recognition for their efficiency and precision builds.
Architects and designers are pushing boundaries, showcasing modular homes as luxurious, sustainable, and architecturally significant. Modern modular homes now boast aesthetic appeal and functional advantages that are competitive with traditional builds. This change is supported by high-profile projects and the adoption of modular methods by well-known architects.
Social media platforms and home improvement shows are playing a pivotal role in reshaping public opinion. They frequently highlight the advantages of modular homes, including their sustainability and speed of construction. Trends indicate a more favorable perception is taking root, as potential homeowners appreciate the benefits of modular construction.
As these positive perceptions continue to grow, the market value and desirability of modular homes are likely to increase. Buyers are becoming more educated about the craftsmanship and sustainability credentials of these homes, which in turn influences their acceptance and demand. It is imperative for industry stakeholders to further educate the public and showcase exemplary modular projects to sustain this perception shift.
Manufactured HUD Housing vs. Modular Homes: Understanding the Differences
In the United States, the terms "manufactured homes" and "modular homes" are often used interchangeably, leading to confusion. However, these two types of housing are distinct in several critical ways, particularly in terms of construction standards, quality, and perception.
Manufactured HUD Housing: Manufactured homes, often referred to as mobile homes, are built according to the HUD (U.S. Department of Housing and Urban Development) code. This federal code sets standards for design, construction, strength, durability, transportability, fire resistance, and energy efficiency. Manufactured homes are constructed entirely in a factory and transported to the site on their own wheels. They are typically placed on a temporary foundation and can be moved if necessary.
Modular Homes: Modular homes, on the other hand, are built to the same local, state, or regional building codes as site-built homes. These homes are constructed in sections, or modules, in a factory setting and then transported to the site for assembly. Unlike manufactured homes, modular homes are placed on permanent foundations and are not designed to be moved once set.