Understanding the Different Types of Prefab Homes
Explore the key differences between manufactured and modular homes, focusing on building regulations, foundations, inspections, customization options, and market perception.
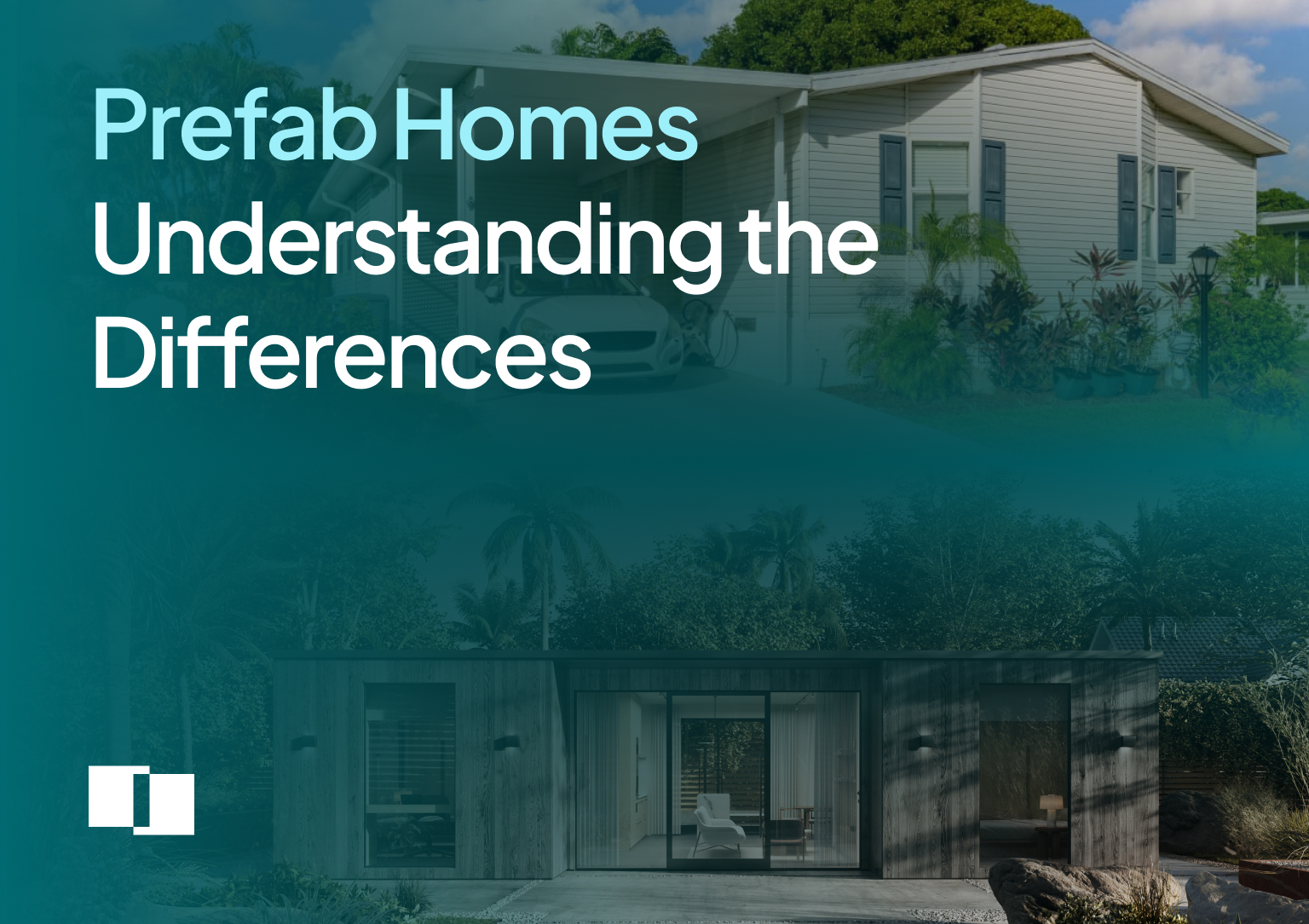
Imagine you're planning to build your dream home but are torn between different types of prefab homes. What sets a manufactured home apart from a modular home?
It's a complex decision.
Prefab homes, encompassing both manufactured and modular options, offer a wide array of benefits tailored to diverse needs and preferences, including being a sustainable and affordable housing solution that can fit various home plans. Prefab homes are built off-site in controlled environments, which significantly reduces construction time and potential weather-related delays. This method also ensures a more consistent build quality and can often result in cost savings due to streamlined production processes. Prefabricated houses have become increasingly popular in recent years, providing a viable and efficient alternative to traditional site-built homes.
Understanding the nuances can significantly impact your choice, both in terms of costs and long-term value.
Building Regulations
Building regulations for manufactured homes are governed by the HUD Code, which establishes standards covering structural design, construction style, fire safety, and energy efficiency, ensuring uniformity nationwide.
Conversely, modular homes adhere to local building codes based on the IBC, modified and enforced by state and municipal authorities, allowing them to accommodate various home plans.
Manufactured Homes (HUD Code)
Manufactured homes are constructed under a federal standard known as the HUD Code. This code ensures uniformity in safety, structural design, and energy efficiency across the nation.
The HUD Code, established in 1976, governs plumbing, electrical systems, fire safety, and more. Compliance is ensured through inspections during their manufacture by HUD-certified inspectors.
Manufactured homes are built entirely off-site and transported to their final location, making them an affordable alternative to traditional homes.
Although typically installed on non-permanent foundations, manufactured homes must meet specific anchoring standards to minimize movement risks. This differs significantly from modular homes, which adhere to more localized building codes and permanent foundation requirements.
Modular Homes (IBC Standards)
Modular homes are highly versatile modern housing solutions.
They are constructed off-site but must comply with the IBC standards. These homes are built in sections that are then transported to the final installation site and assembled there. Unlike manufactured homes, modular homes benefit from compliance with localized building codes, ensuring they meet specific regional requirements.
This compliance boosts their overall quality.
Once installed on a permanent foundation, these structures undergo thorough inspections to ensure adherence to all applicable local codes. This requirement guarantees that modular homes meet safety, structural integrity, and energy efficiency standards similar to site-built homes.
The flexibility of modular homes also allows for extensive customization, making them a sustainable choice for modern housing and diverse home plans. Homeowners can choose from a variety of architectural styles, layouts, and finishes, reflecting their personal preferences and the architectural character of the local neighborhood. This adaptability, combined with rigorous adherence to IBC standards, makes modular homes an attractive and reliable housing option.
Foundations and Installation
Manufactured homes typically utilize non-permanent foundations, incorporating chassis or piers integral to their structure.
These foundations must meet HUD Code anchoring standards aimed at minimizing movement risks, thus ensuring stability. Modular homes, conversely, require permanent foundations akin to those of site-built residences, adhering strictly to local foundation regulations.
The terms "non-permanent" and "permanent" distinguish the level of structural permanence and regulatory oversight.
Non-Permanent Foundations
Manufactured homes often utilize non-permanent foundations despite being residential structures.
The style of foundations used in manufactured homes significantly impacts their stability and functionality. Factors such as the type of soil, climate, and intended usage of the home play crucial roles in determining the most appropriate foundation style. This consideration ensures that the manufactured home performs well under various environmental and situational conditions.
Since 1976, the HUD Code has mandated that manufactured homes meet specific anchoring standards to reduce the risk of movement. Generally, these homes are installed on chassis or piers, providing the necessary support while remaining more flexible than permanent foundations.
This allows for transportation and relocation if necessary, highlighting one of the key benefits of manufactured housing. However, the non-permanent nature can influence the overall stability and longevity compared to modular homes on permanent foundations.
Moreover, non-permanent foundations can affect property valuation and resale potential, often seen as less favorable. Modular or site-built homes on permanent foundations are typically perceived as longer-lasting investments.
Understanding these factors is essential for homeowners to make informed decisions about their prefab homes and other housing options.
Permanent Foundations
Modular homes are placed on permanent foundations.
This approach ensures greater stability and longevity. The foundation must rigorously adhere to local building codes, which are often more stringent to ensure a robust structural integrity. Typically, these foundations are constructed using reinforced concrete, designed to withstand various environmental stresses and provide a solid base for the home.
Inspections ensure compliance.
Once set in place, modular homes experience fewer issues related to settling or shifting due to their strong foundation. This can significantly enhance the home's durability and maintain its value over time.
Moreover, homes on permanent foundations are often more appealing to potential buyers and appraisers, resulting in higher property valuation. Homeowners benefit from a structure that not only meets but often exceeds local building requirements, thereby offering a safe, reliable, and long-lasting residence.
Inspections and Compliance
Manufactured homes are inspected by HUD-certified inspectors during the manufacturing process to ensure compliance with the HUD Code. There is no requirement for further inspection by local building authorities at the installation site.
Modular homes undergo multiple inspections, including factory inspections and further on-site inspections by local building inspectors.
Federal HUD Inspections
Federal HUD inspections are crucial for ensuring that manufactured homes meet national safety and quality standards.
- Performance Standards: HUD inspections verify compliance with structure, plumbing, electrical, fire safety, and energy efficiency performance standards.
- Manufacturing Process: Inspections occur during the manufacturing process, streamlining the path to compliance.
- HUD-Certified Inspectors: Only HUD-certified inspectors conduct these inspections, ensuring expertise and uniformity.
- National Preemption: These regulations preempt local building codes, creating nationwide consistency.
There is no requirement for local authority inspections after the manufacturing process.
This streamlined inspection process allows for quicker installation timelines.
Local IBC Inspections
Local IBC inspections ensure modular homes comply with specific state and local building codes.
- Factory Inspection: Ensures adherence to predefined building codes and standards.
- Foundation Inspection: Verifies the structural integrity and compliance of the foundation with local codes.
- Framing Inspection: Checks the framework of the home to ensure it meets safety and design specifications.
- Mechanical Inspection: Ensures plumbing, electrical, and HVAC systems adhere to local building standards.
- Final Inspection: Assesses overall compliance before the home is approved for occupancy.These inspections are crucial for safeguarding structural integrity and building safety.
By adhering to local IBC standards, modular homes align with the same robust criteria as site-built homes.
Customization and Market Perception
Manufactured homes offer limited customization primarily focused on interior features, while modular homes offer extensive design flexibility, including multiple stories, varied roof structures, and tailored architectural styles. This extensive adaptability allows modular homes to blend seamlessly into diverse neighborhoods, often enhancing their overall appeal and acceptance.
Consequently, modular homes generally enjoy a more favorable market perception and often appreciate similarly to site-built homes. This contrasts with manufactured homes, which may depreciate more rapidly.
Design Flexibility
Design flexibility is a critical consideration when choosing between manufactured and modular homes.
Style plays a crucial role in the overall perception and market value of modular homes. The ability to choose and design different architectural styles allows homeowners to personalize their living spaces to their liking, making each modular home unique. This customization contributes to higher satisfaction among homeowners and can positively impact the home's resale value, as more buyers may be attracted to well-designed, aesthetically pleasing homes.
For manufactured homes, the scope for customization is relatively narrow, largely confined to interior finishes, style, and fixtures. The HUD Code's stringent guidelines often limit structural modifications, which means exterior design elements and floor plans are more standardized and less adaptable. This can lead to a uniform appearance across many manufactured homes, constraining architectural uniqueness.
Conversely, modular homes shine in their modern versatility, offering extensive design options. Builders can create modular homes in virtually any architectural style, allowing for customization in both exterior aesthetics and interior layouts. This flexibility enables homeowners to achieve a personalized home that meets both functional needs and aesthetic preferences, more closely resembling traditional site-built homes.
Moreover, modular homes can accommodate more complex architectural features and multi-story designs, providing a higher degree of creative freedom. This design adaptability not only allows for a unique, tailor-made home but also facilitates better alignment with existing neighborhood styles, significantly enhancing curb appeal and market acceptance.
Resale Value
The resale value of prefab homes can differ significantly based on their type and construction standards.
Manufactured homes often face resale value challenges.
These homes may depreciate in value more quickly due to their non-permanent foundations and limited customization options.
In contrast, modular homes tend to retain their value better, partly because they are built to the same standards as traditional site-built homes. This similarity can enhance their longevity and market perception, often making them more desirable in the real estate market. Additionally, because modular homes offer greater architectural customization and adhere to local building codes, they are generally viewed as more permanent and of higher quality, which positively influences resale value.
When it comes to market perception, modular homes generally enjoy a more favorable reputation compared to manufactured homes. Modular homes are often seen as comparable to site-built homes in terms of quality, longevity, and resale value, making them an attractive option for discerning buyers. In contrast, manufactured homes, frequently stigmatized as "trailer park homes," suffer from a negative perception due to their association with lower build quality and less desirable locations. This stigma is compounded by the fact that manufactured homes are typically found in areas that lack the appeal of custom home neighborhoods where modular homes can be constructed, further influencing their market value and desirability.
In Summary
Prefab homes, encompassing both manufactured and modular homes, offer diverse housing solutions but differ significantly in terms of building codes, foundation requirements, inspections, design flexibility, energy efficiency, and market perception. Manufactured homes adhere to the federal HUD Code and are often installed on non-permanent foundations, while modular homes comply with local building codes, similar to site-built homes, and are placed on permanent foundations. Modular homes offer greater customization, higher energy efficiency, and better market perception compared to manufactured homes, which are often stigmatized as "trailer park homes" with lower build quality and less desirable locations.
Ikkonic provides beautifully designed homes built to the highest standards of quality and energy efficiency. Explore our predesigned and customizable options for modular homes and ADUs at ikkonic.com/models.